Proton Paper is Manufacture of Duplex Paper Board in INDIA
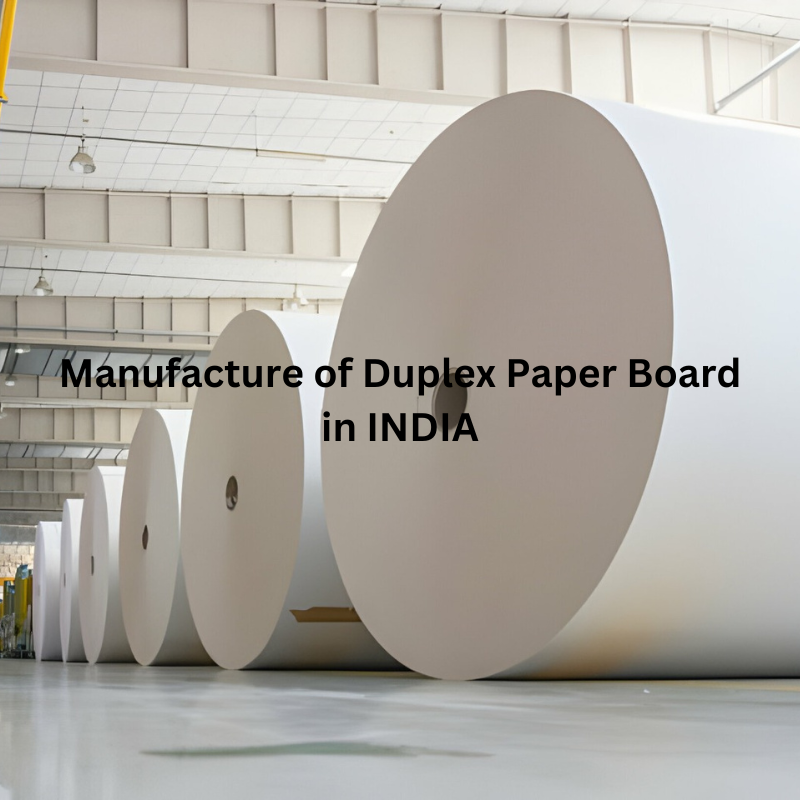
Raw Material Preparation:
Pulping:
- It starts with making a pulp which can be either from virgin or recycled fibers. Pulp selection depends on the required quality and use of duplex paper. The inner layer is more like recycled paper and the outer ones are comparatively of higher quality using virgin pulp.
Mixing Pulp:
- The pulp is mixed with water and other chemicals to make slurry for paper making. Can also include such as sizing agents, fillers and binders to enhance the strength or printability properties of paper.
Forming the Base Layers:
Duplex Paper has 4 Layers:
- The inner layer usually made of recycled pulp, then is laid on 4 wire section of the papermaking machine. And then an outside layer of typically bleached virgin pulp, which provides the smooth white deliverable line.
Pressed and Bonded:
- The layers are then pressed, which removes the extra water and bonds the sheets together. Pressing also helps smooth the paper and create an optimum thickness.
Coating of paper:
Coating:
- The surface properties of duplex paper board are usually coated with various types of coatings, which can improve the gloss, smoothness and printability. This is usually made with a mixture of clay and calcium carbonate on the outside while containing various other chemicals
Drying:
- Once the coating is applied, the paper travels to drying cylinders or infrared dryers that deliver high temperatures and then moderate heat levels for elimination of excess moisture in addition to properly setting the coat. This step is very important to get the surface finish and print quality that you want.
Calendering:
Smoothing:
- Calendering is the process of putting a paper through various heated rollers to compress and smooth out its surface. This makes the paper more smooth and keeps a thickness on its surface.
Caliper Control:
- The calendering process also controls the final thickness of the duplex paper, so it is well-suited towards usage in something like packaging or printing.
Cutting and rewinding process:
Slitting:
- The final duty of the manufacturer is to reduce large rolls and at last completed duplex paper sheets are into smaller sections or larger parts in accordance with the client’s demanded size.
Quality Control:
- Testing – Various standard tests are performed at different stages of manufacturing to ensure that duplex paper board is as per required standards. It is for testing the strength, thickness and evenness as well as printability.
Final Check:
- Just before packaging, a final check is done to ensure that there are no errors or on the paper.
Packaging:
- Wrapping:
- The end rolls or sheets of the duplex paper are wrapped with plastic protective materials so as to not damage its surface by during transport and storage.
Labeling:
- Labeling is critical for a product to be recognized and traced through the entire supply chain.